Insulated vs Non-Insulated Terminals: A Comprehensive Comparison
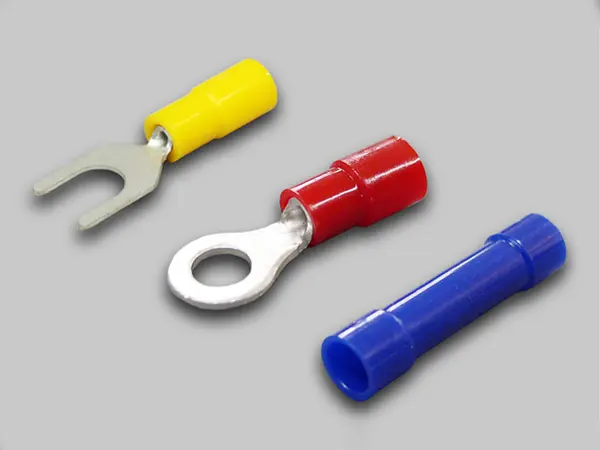
When it comes to electrical connections, choosing the right terminal is crucial. The main distinction between insulated and non-insulated terminals hinges on the existence of an insulating layer surrounding the metal connection point. Understanding the features, pros, and cons of each type can help you make an informed decision for your electrical projects.
Insulated Terminals: Safety and Reliability
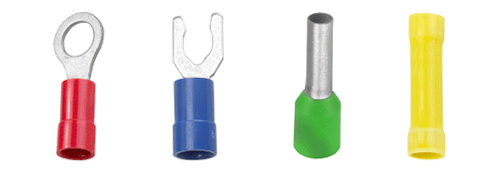
Insulated terminals are designed with an added layer of protection, usually made from materials like PVC or nylon. This protective coating serves multiple purposes, acting as a safeguard against electrical shorts, reducing the risk of electrical shocks, and preventing corrosion.
Function
The primary function of insulated terminals is to enhance safety and reliability in electrical systems. By providing a barrier between the conductive metal and its surroundings, they ensure that electrical current flows precisely where it's intended, minimizing the chances of accidental contact or short circuits. This makes them an ideal choice for applications where safety is of utmost importance, such as in automotive wiring, household electrical systems, and industrial equipment.
Design
Typically, insulated terminals feature a plastic or rubber coating around the metal barrel where the wire is inserted. This coating not only offers insulation but also provides mechanical protection to the connection. Some insulated terminals, like heat shrink insulated terminals, can even form a tight seal when heated, further protecting the connection from moisture, dust, and other environmental factors.
Advantages
- Enhanced Safety: The insulating layer significantly reduces the risk of electrical accidents, protecting both users and equipment.
- Environmental Resistance: They are better equipped to withstand harsh environmental conditions, ensuring a longer lifespan for the connection.
- Reliable Performance: With proper installation, insulated terminals offer a more stable and consistent electrical connection, reducing the likelihood of intermittent failures.
Disadvantages
- Higher Cost: Due to the additional insulating material and manufacturing processes, insulated terminals are generally more expensive than their non-insulated counterparts.
- Space Requirements: The extra insulation may require more space, which can be a limitation in applications with tight wiring constraints.
Examples
Popular types of insulated terminals include vinyl insulated terminals, nylon insulated terminals, and heat shrink insulated terminals. Each type has its own unique properties and is suitable for different applications based on factors like temperature resistance, flexibility, and durability.
Non-Insulated Terminals: Cost-Effective and Space-Saving
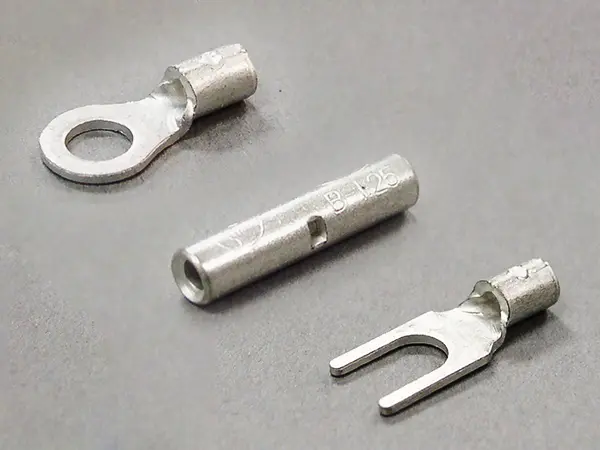
In contrast, non-insulated terminals are made entirely of metal, lacking any insulation on the barrel. While this makes them simpler in design, it also means they require more careful handling during installation to avoid potential issues.
Function
Non-insulated terminals primarily serve as a conductive link between wires or other electrical components. They are designed to provide a secure electrical connection without the added layer of insulation, making them suitable for applications where insulation isn't necessary or where space is at a premium.
Design
These terminals are typically constructed from metals like copper or brass, which offer excellent electrical conductivity. Their simple, all-metal design allows for easy insertion and crimping of wires, making the installation process quick and straightforward.
Advantages
- Lower Cost: Without the additional cost of insulation materials, non-insulated terminals are more budget-friendly, making them a popular choice for large-scale projects or applications where cost is a major consideration.
- Space Efficiency: Their compact design makes them ideal for use in tight spaces where bulky insulated terminals may not fit.
Disadvantages
- Risk of Shorts: Since they lack insulation, there is a higher risk of electrical shorts if the terminals come into contact with other conductive materials or if the installation isn't done properly.
- Corrosion Vulnerability: Non-insulated terminals are more exposed to the elements, increasing the likelihood of corrosion over time, which can affect the integrity of the electrical connection.
Examples
Common types of non-insulated terminals include ring terminals, spade terminals, and lug terminals. Ring terminals are often used for grounding applications, spade terminals are suitable for quick disconnects, and lug terminals are commonly used for heavy-duty electrical connections.
In conclusion, both insulated and non-insulated terminals have their own unique advantages and are suited to different electrical applications. When choosing between the two, consider factors such as safety requirements, budget constraints, available space, and the specific demands of your project. By understanding the differences between these two types of terminals, you can ensure a safe, reliable, and efficient electrical connection.